7 Finishing Options for Your Metal Products
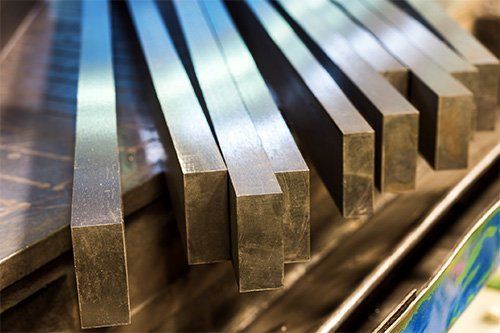
You might struggle to choose a metal finish because of the sheer variety of finishes and finishing processes available. Nonetheless, here are some of the most common finishing options to help you enhance the aesthetic and structural properties of your metal products.
1. Polishing
Polished metal products have an attractive reflective finish, are rust-resistant and more durable, and conduct electricity better.
For small, customized orders, providers may hand-polish metal products. However, advances in robotics and automation now allow faster and more precise metal polishing using hi-tech machines.
2. Buffing
Consider buffing if having smooth edges for your metal product is a priority. The buffing method can help to add an element of luster to your metal goods, but due to the rigorous process, this may not be the best finishing procedure for fragile products or products with intricate features.
3. Plating
Common metals for electroplating metal products include nickel, zinc, copper, and tin. Each metal has its own advantages. You may also elect to electroplate your metal products using precious metals such as palladium, gold, or silver.
Precious metal finishes are more resistant to corrosion, have higher thermal and electrical conductivity, and can enhance the durability of the underlying metal. However, expect to pay more for electroplating with precious metals.
4. Electro-Coating
Electro-coating provides an even paint finish and is an excellent alternative to conventional painting methods. Like electroplating, this process uses an electric current to coat a metal product with epoxy paint, which can protect against abrasion and corrosion.
5. Blasting
You can use blasting as a finishing on its own or as a surface preparation method for an additional finishing process such as painting or electroplating.
6. Grinding
This intense method entails the use of machines to apply pressure and friction to smooth out a metallic surface. Metal technicians use different machines to achieve different levels of smoothness according to customer preference.
7. Brushing
The brushing method sands the metal surface and then smoothens it out to achieve a muted appearance. The downside is that brushed metal surfaces are more prone to corrosion.
When deciding the type of finish to use for your products, consider factors such as the type of metal, the costs, and your own lead-time. Consult with your welding contractor about the most suitable finishes for your type of metal goods.
If you are looking to build a metal product for residential or commercial purposes, you need a welder you can trust to get the job done right from start to finish. At Sam's Welding, Inc , we have the expertise, experience, and resources to transform your metal project into reality. Get in touch with us today to learn more about our welding and fabrication services.